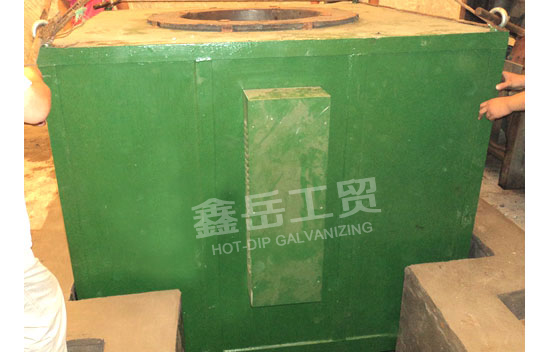
Design and Construct Hot Dip Galvanizing Plants both Domestically and Internationally
Add: Jinshan Bridge Zone, Xuzhou, Jiangsu, China
Mobile: 86-13805211808
Tel: 86-516-83168088
Email: xy-rjd@163.com
The zinc pot is indispensable key equipment with high value and easy consumption in the hot dip galvanizing production. The greater part of the previous traditional zinc pots are made of special steel products (05F, 08F, industrial pure iron, etc) by welding method or cast iron. With the rapid growth of the national economy, the zinc consumption for hot galvanizing production has increased from 15% of zinc output 10 years ago to more than 45% of that now. According to incomplete statistics, the all zinc pots at home is estimated as 5000-6000 pieces. Because the high value and easy consumption of zinc pot decreases the economic benefit of hot dip galvanizing factories considerably, how to find a new substitute for it is very important for hot dip galvanizing factories and also a difficult problem to be solved necessarily for many engineering and technical personnel in hot dip galvanizing field. Through the common effort of many scientific and technical personnel of our company during some years and on the basis of investing a lot of funds and repeating tests, Xinyue Company has developed the “industrial ceramic” zinc pot with external heating function and solved the difficult technical problem successfully. The “industrial ceramic” zinc pot can be heated with many heating modes: Regardless of coal, oil, gas and electric power, they can be used for heating and its brickwork is simple. The new ceramic pot not only prolongs the working life of it, but also decreases 30%-40% of zinc slag. The zinc consumption / tonne of product has decreased from 70-100 kg to 40-50 kg (dip galvanizing of cast iron). The “industrial ceramic” zinc pot in some galvanizing factories has got a very good economic benefits successfully and is well received by many customers. Because of large difficulty of technology and manufacture, at present only column shape ceramic pot with maximum size ofф800×1100 and 2.5 tonnes of molten zinc can be made. The rectangle pot is being tested. It is believed that ceramic pot will replace metal that in the near future.
Applicable scope:
At present, “industrial ceramic ” pot can be widely used for the dip galvanizing of malleable cast iron, cast iron and steel, various metals, steel structural parts and other small pieces and is substitute for original cast iron pot of small galvanizing factories.
For larger galvanizing factories, the smaller galvanizing work pieces are also produced. In this case, if large pot is used in production, time and human resource will waste, and cost will be too high. If ceramic pot is used, the zinc slag and ash collected from the large pot are melted again at 620℃ and so a lot of quality zinc are recycled. The small work pieces is galvanized at the temperature and it assures the product quality, considerably decreases overall zinc consumption as well as widens product market. The feedback information from many customers shows: the profit produced by a ceramic pot with 3-5 operators is almost equal to all wages and salaries of the employees in one factory.。
The recommended product will give considerable profit to your enterprise.
Technical index:
Owing to the electrochemical corrosion of steel body by molten zinc, the zinc consumption and zinc slag amount increase notably and the life of zinc pot decreases considerably in many galvanizing factories using steel galvanizing zinc pot. The “industrial ceramic” is an optimum method to avoid the corrosion by high temperature molten nonferrous metals media.
Industrial ceramic should satisfy the following technical requirements:
Compact structure, integrity, without pores and non-permeation for media:
High hardness, wear resistance and corrosion resistance;
Excellent thermal capacity and heat conductivity.
Item |
Industrial ceramic |
|
Zinc-corrosion resistance |
good |
|
Thermal conductivity |
20℃ |
18.5 |
(w/m·K) |
1000℃ |
16.5 |
Softening temperature(℃) |
Without softening at 1700℃ |
|
Bend strength |
20℃ |
80 |
(MPa) |
1300℃ |
100 |
Average specific heat (Kcai/kg·℃) |
0.29(20-1400℃) |
|
Moh’s hardness |
9-9.2 |